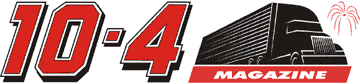
Tech Tips
and Tid Bits...
BUILDING THE BEST, ONE AT
A TIME
A LOOK AT WHAT IT TAKES TO
MAKE A VALLEY CHROME BUMPER
By Daniel J. Linss - Editor

For almost fifty years, Valley Chrome
Plating (VCP) has been a respected manufacturer of quality products for
the automotive and trucking industries. Since about 1990, VCP has been
focusing entirely on aftermarket bumpers for big rigs – specifically,
custom bumpers built to order for each customer. They are certainly not
the biggest bumper manufacturer out there, but they are the best, hands
down. Just ask any trucker out there with a nice rig where he got his
bumper – nine times out of ten he’ll answer, “Valley Chrome made it for
me.” The other one time they’ll probably answer, “I made it myself.”
Valley
Chrome Plating, Inc. was started as a small chrome plating shop near Alturas,
California in the late 1950’s. In 1960 the company moved to Fresno, California.
In 1961, Anthony Lucas and his wife Claire (and six children) came to
California from Indiana to join his brother Chuck and another partner
in the business. Anthony forwarded his life savings ($12,000) and bought
into VCP sight unseen. A few years later, Anthony bought out his two partners
and became the sole proprietor of VCP.
In the early days of the company,
VCP plated just about anything. Metal furniture, sprinkler heads, hitch
balls, wheels and gym equipment were just a few of the various items they
plated. Valley Chrome began automotive bumper recycling to augment their
plating business. Around 1967, a local Fresno trucker came to the shop
and asked if they could build him a wide bumper for his Kenworth. Never
afraid of a challenge, they agreed and then painstakingly hand-made him
a 16-inch bumper for his truck. Pretty soon they were making two or three
custom bumpers (by hand) a week, and then two or three a day, etc. From
there, it just kept growing. No one really knows where the term “Texas
Style” bumper came from (it probably had something to do with the fact
that everything in Texas is big), but one thing is for sure - the first
“Texas-Style” bumper was built by VCP in Fresno! In March of 1980, the
company moved from Fresno to its current location in Clovis, California.
Around
1990, VCP discontinued all other aspects of their business and began to
focus entirely on manufacturing truck bumpers. Since then, the company
has grown tremendously. They now service a network of hundreds of dealers
that stretches across the United States and Canada. Today, their 75-employee
work force, operating out of two side-by-side buildings in Clovis, California,
builds and ships about 150 custom-ordered bumpers a day. Customers can
choose their bumper’s style, width, light arrangement, and a host of other
options. We were told that there are over 10,000 different configurations
available.
Valley Chrome has always been a family
operation, and today the company is run by six of Anthony’s eight children.
Anthony retired about ten years ago due to medical reasons. Each sibling
has a specific niche or expertise, and each one allows the others to have
their space. Anyone who has ever worked with family knows it’s not always
easy, and this family is no different. They have their occasional squabbles,
but in the end, they work it out. In addition to the six brothers and
sisters, VCP is also lucky to have a few “lifers” that might as well be
part of family – namely, Kent Carpenter and Lee Misakian (photo 2).
The
oldest boy, Ray Lucas, carries the title of president. He started out
working in the shop in 1967 while still attending high school. Ray was
put in charge of the night crew and Kent Carpenter was one of the first
guys he hired. Ray’s specialties are plating, problem-solving and environmental
issues. Ray’s younger brother Tom is the vice president and CFO. Tom handles
all the accounting and is known for always seeing “the big picture.” Their
sister Cathy is the treasurer. Her niche is collections. She is good at
getting people to pay the money they owe. Greg is in charge of production
and oversees the plant. Greg handles all the research and new technology
and is known for being an efficiency expert. Christine is in charge of
human resources – she handles all the employees. Matt, the youngest of
the bunch, was brought in a few years ago to head their safety department.
Plating is a dirty and dangerous job, and its Matt’s responsibility to
make sure that nobody gets hurt while working there.
Although
not a member of the family, Kent Carpenter has been around longer than
most of the Lucas siblings. Kent started out at VCP in 1969 working part
time on the night crew while still going to school. After he graduated,
he started working full-time. At that time, VCP was just one of his three
jobs. Kent worked at a hardware store in the day, VCP at night and a gas
station on the weekends. Kent helped the company put together their network
of dealers and today he heads up their sales department. You’ll find Kent
at about every major truck show in the nation, always talking, always
looking for a fun time. Another longtime employee is Lee Misakian. Lee
started in 1975 as a welder. Today, he is the shop manager and lead programmer.
Over the years, Lee has written almost all of the computer codes for each
option available (over 10,000 of them). But enough about the people that
make up Valley Chrome, let’s look at what it takes to build a chrome-plated
truck bumper.
Every
bumper starts out as a flat sheet of raw steel, or whatever material is
being used (photo 3). First, the sheet is cut into the shape of the bumper
by a computer-programmed plasma cutter (photo 4 shows a few stacks of
cut sheets). Next, the appropriate die is chosen and inserted into a 400-ton
press and the flat bumper is “pressed” into shape (photo 5). Then, the
bumper is inspected and welded where needed (photo 6). From there, the
bumper is placed into a laser cutting machine (photo 7) and all of the
necessary holes are cut and any custom engraving is done (photo 1 shows
an engraved bumper). Now the bumper is ready to be plated.
Each
bumper is polished prior to plating to provide a better finished product.
Like painting, the quality in plating comes from the prep work. Chrome
plating is only 1/1000th of an inch thick, so you have to thoroughly prepare
the surface before plating. First, the bumper is dunked into several cleaner
tanks, then it goes through a few rinse tanks filled with fresh water.
Then it goes into an acid tank that microscopically “roughs up” the steel
which helps the plating stick. Then it goes through a few more rinse tanks.
This entire clean, rinse, acid and rinse again cycle is repeated before
the bumper is finally placed in the plating tanks (there are a lot tanks
on the plating line).
There
are three steps in the plating process. First, the bumper is plated with
dull nickel, then with bright nickel, and finally, with chrome. The bumper
spends about 30 minutes in each nickel tank and then about 4 minutes in
the chrome tank (photo 8). To finish the process, the bumper is cleaned
and polished by hand and then checked one more time for flaws (photo 9).
From there, the completed bumper is placed on a rack with wheels (photo
10) and then taken to the warehouse to be prepared for shipping.
VCP is known for running a “clean”
shop – so much so that Ray is asked to speak on the subject to other plating
companies across the country about their policies and procedures. Ray
is currently the Secretary/Treasurer for the National Association of Metal
Finishers and is very active in that arena. In 1999, VCP became a zero-discharge
facility, which means nothing goes down the drain at their facility except
for sanitary (bathroom) water. Ray designed and built a series of machines
that utilize Ion Exchange Technology and put VCP on the map as one of
the first plating companies to recycle their plating solution instead
of having to landfill it as waste. In the early days, before regulations,
the rinse tanks were drained all the time – but not anymore. Thanks to
their advanced recycling systems, the water in their rinse tanks has not
been replaced since the late 1980’s! Ray is very proud of the accomplishments
they have been able to achieve in the area of environmental safety. Their
shop sets the standard that most other shops strive to match.
Currently,
Valley Chrome’s facility includes two buildings with a total of about
34,000 square feet. Thanks to booming business, they recently realized
that they had outgrown this space so they began work on a third building.
The new structure will be about 32,000 square feet and, basically, will
double their space (photo 11). Earmarked specifically for manufacturing,
this innovative new building will be bright and well-ventilated, and should
help them to significantly increase their production schedule.
Never
afraid to try new things, VCP recently began marketing truck accessories
besides just bumpers. Last year they dabbled in the wheel spinner market
and, currently, they are marketing a product called the Tower Lite, which
is a lighted floor plate that provides a soft glow around your shift boot.
Presently, they are having these items made by other companies, but, with
their new building, they should be able to start manufacturing these items
on their own. One of their goals is to eventually have an entire line
of truck accessories, and to make them all in-house. If all goes as planned,
they should be in the new building later this year.
So,
if you didn’t already know, now you do. If you’re looking for a quality,
custom bumper, there is no need to think about who to call. Get in touch
with a local chrome shop that sells Valley Chrome bumpers and get what
you need – just the way you want it. And if you want something different
or extreme, don’t be afraid to ask. And not only do they make a great
product, but they are some of the nicest people you’ll ever meet. For
more information or to locate a dealer, visit www.valleychrome.com
or call (800) 354-0976.
Copyright ©
2005 10-4 Magazine and Tenfourmagazine.com
PO Box 7377 Huntington Beach, CA, 92615 tel. (714) 378-9990 fax
(714) 962-8506
|